Automotive Parts
In the automotive parts industry, every single component impacts the speed and quality of customer service.
LOGISPOT supports optimized logistics flows with real-time inventory management, delivery tracking, and integrated data visibility
—enabling quick response to customer needs.

실시간
재고관리

통합 데이터
관리 기능
Logistics Characteristics of Automotive Parts Delivery
Manual dispatching through Excel, phone, and email, along with outdated inventory control methods, can no longer support the precision and efficiency required in today’s parts logistics.
Automotive Parts

Diverse part types
Requires precise classification and management of thousands of parts with varying sizes and weights
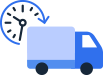
Urgent delivery needs
Fast and accurate delivery is critical to support timely repairs at service centers and garages

Real-time inventory and tracking
Operators must monitor part locations and inventory movement in real time to ensure smooth operations

Complex logistics network
Distribution spans multiple nodes—from manufacturers and warehouses to service hubs and garages
LOGISPOT’s Delivery Solution for Automotive Parts
Automotive parts logistics demands real-time control over fast delivery deadlines,
accurate inventory, and complex distribution networks.
LOGISPOT enables full visibility into inventory movement, delivery status, and order flow through its real-time, data-driven logistics platform.
Real-Time Transport and Inventory Management
- Integrated management of transport requests, dispatching, and inventory movement in one platform
- Real-time visibility into delivery status and inventory flow
Automated and Efficient Transport Operations
- Seamless API integration with ERP systems for automated transport requests and settlement
- Group-based settlement functions for easy management of warehouses and regional hubs
Data-Driven Logistics Optimization
- Structured data management through delivery code matching
- Identification of cost-saving opportunities using transport and inventory data
User-Friendly Interface
- Easy-to-use, intuitive UI/UX for all users
- Role-based access controls and dashboard statistics for personalized operations
Cost Reduction and Productivity Improvement
- Delivery delays minimized through driver capacity management and optimized dispatch
- Preventive control over issues like stock shortages and delayed shipments leads to higher customer satisfaction
Customer Case Study
From Inefficiency to Innovation in Automotive Parts Logistics — Powered by LOGISPOT
LOGISPOT provides an integrated digital logistics platform designed to solve the complexities of automotive parts logistics. Previously, the client companies were managing part deliveries between service centers and nationwide partner repair shops through phone calls, emails, and Excel files—resulting in operational inefficiencies. Since adopting LOGISPOT, they have achieved real-time visibility into transportation and inventory flows, significantly improving information management, speeding up delivery, and increasing customer satisfaction.
Client K
Challenges Before LOGISPOT
- Dispatch requests were handled manually via Excel, phone, and email, leading to delays and high coordination effort
- No centralized system for tracking inventory movement or delivery history
- Managing settlement-related data was manual and inefficient
After LOGISPOT
- Automated transport and inventory system
Simplified workflows by managing part movement requests on a single platform - Real-time inventory and delivery tracking
Enabled inventory traceability through ERP integration and item-level data input - Improved settlement efficiency
Group-based settlement functions enabled cost allocation by warehouse - Owner-operated vehicle use and warehouse efficiency consulting
Identified cost-saving opportunities and reduced operating expenses
Client H
Challenges Before LOGISPOT
- Parts were delivered from 18 regional warehouses to 780 partner repair shops nationwide → Only one owner-operated vehicle per warehouse caused frequent delivery delays
- Manual dispatching via Excel and phone Staff experienced heavy workloads due to inefficient assignment processes
- Delivery delays led to an increase in customer complaints(VOC)
- Real-time visibility into inventory locations was not available, making it difficult to track part movement
After LOGISPOT
- Delivery requests simplified
Real-time monitoring and auto-dispatch minimized delays - User convenience improved
Platform streamlined workflows and reduced staff burden - Inventory tracking digitized
Real-time updates and admin alerts during inventory movement - API integration enabled
Analytics features added and request handling simplified