CPG (Consumer Packaged Goods)
Leveraging our nationwide logistics infrastructure and extensive experience with major domestic CPG brands,
we ensure reliable product delivery that enhances both brand value and consumer satisfaction.

전국
네트워크 및 인프라

CPG 기업
물류 운영 경험
Logistics Characteristics of CPG
CPG logistics involves a complex process to ensure mass-produced consumer goods are delivered swiftly to consumers across the country.
It requires efficient management of diverse product lines while consistently maintaining brand image and quality throughout every step of the supply chain.
CPG

High-Volume Operations
Due to the bulky and fast-moving nature of consumer goods, efficient storage and transportation are essential

Complex Distribution Networks
Logistics must support multiple sales channels simultaneously, each requiring tailored operations

Demand Volatility by Season and Trends
Flexible response to rapid demand changes driven by seasonality and promotional campaigns is critical

Inventory Optimization
Accurate forecasting is required to avoid overstock or stockouts

Consistent Quality Assurance
Uniform quality must be maintained across all regions nationwide
Tailored, Integrated Logistics Solutions for CPG Products
PANASIA LOGITECH, a LOGISPOT family company, successfully manages logistics operations for many of Korea’s leading CPG brands.
With nationwide coverage and solutions tailored for CPG distribution, we ensure fast and secure delivery from warehouse to end-consumer.
POINT 01
Stable Workforce and Equipment Management
- Experienced logistics specialists with over 10 years of field expertise
- High ratio of dedicated staff ensures service consistency and rapid response
- Professional equipment operations and optimized fleet management enhance service stability
POINT 02
Systematic Inventory Control
- WMS-based inventory tracking enables fast fulfillment and higher customer satisfaction
- Real-time stock monitoring provides full operational transparency
- System-driven picking and inspection processes reduce shipping errors
POINT 03
Cost Reduction and Operational Efficiency
- Long-term cost efficiency through dedicated fleet and workforce
- Optimized routing and workflows reduce logistics expenses
- Streamlined operations maximize overall process efficiency
POINT 04
End-to-End Integrated Logistics Solutions
- From warehouse operations and equipment to fleet management and delivery, we offer integrated logistics that cut costs
- Complete solutions from initial warehouse infrastructure setup to daily operations
- Flexible response to seasonal demand fluctuations and promotional spikes
- Custom-designed logistics processes tailored to the unique needs of CPG products
Customer Case Study
“Logistics Innovation for High-Volume CPG:
A Fully Integrated, End-to-End Solution”
Since 2014, a leading household goods manufacturer has partnered with us to handle logistics for tissue, sanitary products, and hospital supplies across the Seoul metro area, Yeongnam, and Chungcheong regions. As the company expanded its product lines and sales channels, the need for a more efficient logistics framework became urgent.
Challenge
Managing the Complexity of High-Volume
CPG Logistics
- Bulky Goods Handling
Needed an optimized system for storing and moving large, heavy items - Multi-Channel Distribution
Required tailored services for retailers, convenience stores, and online platforms - Seasonal Volume Fluctuations
Needed to maintain service stability during peak seasons and promotions - Inventory Accuracy
Faced difficulties with real-time stock visibility and bulk inbound/outbound control
Solution
Expertise-Driven Integrated
Logistics System
- Skilled Workforce
Deployed logistics professionals with 10+ years of CPG experience to establish a stable operating system - Specialized Equipment Operations
Maximized efficiency with professional logistics equipment tailored to product characteristics - WMS-Based Inventory Services
Provided FIFO control and customized inventory management via WMS, offering picking, packing, and delivery services tailored to channel-specific requirements - Flexible Labor Model
Balanced fixed and flexible workforce for optimal responsiveness to volume fluctuations
Results
Operational Innovation Through Workforce, Equipment, and Systems
- 20% faster order processing
through skilled labor and specialized tools - 10% logistics cost reduction
through optimized manpower and resource use - 15% drop in operational errors
via systemized workflows and barcode scanning - 99% on-time delivery rate
through stable order fulfillment systems - 0.01% inventory shrinkage
achieved through quality control - 50% improvement in peak-season handling capacity
enabled by a flexible workforce and scalable systems for stable service delivery
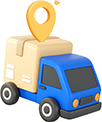
“Since partnering with PANASIA LOGITECH, our company’s complex logistics environment has seen a dramatic transformation thanks to their professional workforce and structured systems. The storage and handling of bulky consumer goods have become much more efficient, and their accurate inventory management system enables fast, reliable fulfillment—resulting in a significant boost in customer satisfaction. Their ability to maintain stable service during promotional events and seasonal demand spikes is a key strength. With consistent logistics quality ensured by expert staff and well-managed equipment, we’ve been able to reduce our logistics burden and focus more on our core business.”
Client A, Head of Logistics